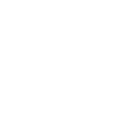
0
Messages blinking
System: MD4-5 + MC43 + XC43, Design version 6.02 -> 6.04.9.
All messages (warnings, alarm, info etc.) are blinking on display IF there are more than 1 message.
Customer support service by UserEcho
System: MD4-5 + MC43 + XC43, Design version 6.02 -> 6.04.9.
All messages (warnings, alarm, info etc.) are blinking on display IF there are more than 1 message.
Customer support service by UserEcho
Are you using the System dialog boxes Deactivation property?
If you look in the system logs for the two masters that have the errors, do you see them filling up with multiple entries, as if the errors are cleared and then triggered again ?
I set Deactivation to "No", like your message is. Now messages doesn't blink, but messages pop up again imediately after you close those. Log files full imediately with same erros, after you clear the log.
Best way to troubleshoot is to use IQANrun and graph the channels that are having the errors.
In the graph, you will be able to see the status on the channels.
The message and the log entry comes up when the channel status change to Error.
As the messages keep popping up and they fill up the log, either the channel is OK or Disabled in between.
If the application has some functionality that disable and enable function groups in runtime you could have the effect that it changes between disabled and error.
Or it could be that the error goes away so that it is OK for a brief moment, and then comes back.
I notice the input that has low error is a current loop input. Is it a regular 4-20 mA sensor? How is its min current calibrated?
Don't worry about me. I can set errors off. But problem is when system goes to our customers who don't have knowledge or Iqan Run. When these errors pops up as soon as you close those, you can't even go to menu where to set these inputs off! You should change Iqan that even errors appears full time, customers could turn those off in MD4 display. Error logs can save these errors continously, but display shouldn't show these full time.
Normally with an error like this the customer would not continue using the machine until it is repaired.
If you want for him to be able to hide the error there are many ways you could do this yourself in your program.
For example make a channel that disables the function group containing the pressure sensor when there is an error.
At this case we use pressure sensors in these error inputs. These sensor values are used only for optimizing system performance. Without sensor value system use standard values and machine can still running. So customer could continue working without these sensor inputs. Otherwise in worst case, customer have wait days to get new sensor or service man and machine is down at this time.
I have made an option value to turn these inputs off (function group inputs disabled / enabled). But how can customer go to menu system to turn these inputs off when error is continously on? (you can't click menu button on MD4 if error message is displayed)
You can make a channel that detects when there is an error on an input using the status feature.
As soon as that channel goes true you disable the function group with the input and make a log entry
Of course you should have a latching function for this outside the function group that can then be reset with a menu or reboot.
Thank you for your advice. I will try that.
Still, I think that Iqan team should do something for this continuos Error messages pop ups on displays. I have used Iqan systems about ten years and this is first time when I notice this kind of problem!
When you click error close, then same error should appear after some time, not immediately.
As Gustav explained above, it most likely reappears because of your programming.
Somehow the channel goes into non-error state for a short while and then to error again.
You can try to make a new program with just one input and then disconnect the sensor. You will see you can close the error message and it will note come back unless you plug the sensor in and out again.
I made new blank program. No code inside, only sensor inputs. Still same problem. Also simulator does not behave like this. Is this still "my programming fault"?
You have set the Min value to 4 µA. This is basically almost zero. 0,004 mA.
Just the lights flickering in your house with 50Hz will make the error disappear and reappear 50 times per second causing the error message to retrigger like it does and your scaling will be wrong.
Change Min to 4000 and Max to 20000.
"Current-loop in channel (CIN)
Physical analog input. The current-loop input channel is used to measure analog sensors, for example temperature, pressure, angle, position, etc.
The unscaled range is 0 - 20000 µA, the scaled range is application dependent."
It says that minimum value can be from 0 -> 20000µA
If you have Voltage sensors (inputs) and you set minimum to examble 1-5mV (for some reason), why it does not behave same? On voltage channel Erros are not popping up full time, you click those and then they are gone.
If you look in the manual you will see that the input circuits for current input and voltage input are quite different. The voltage input has a constant 32 kΩ pulldown resistor to ground which would prevent external noise from generating 5mV.
Also 5mV is 1/1000 of the full scale.
4µA is only 2/10000 of the full scale, much closer to the noise floor, probably close to 1 bit of the ADC.
So not a bug, Just need to know. Stupid me :(
Every day that we learn something is a day that we got smarter :)
Maybe you could update simulator to work same way like real world. Then you could notice this kind of mistakes sooner? Or make system to foolproof for users like I am :D
I finally got my new sensor to test. These mA sensors signal wobble a lot. Is this normal (about +/- 15bars)? I have only experience from mV sensors and those are not behaving like this. If this is "normal" behaving, we have to change back to mV sensors.
Read the datasheet of your sensor. If it says for example 0.1% repeatability that means it should not fluctuate more than 0.6 bar.
I would think something is wrong with your power supply, connections, sensor or iqan module.
Easy to test it separately with a multimeter and battery.
Repeatability is < 0.5% and it is connected to Vref so power supply should be stable. In same connector have voltage sensors and those are working. I have to make more test on next week.
According to the manual, current sensors are recommended to be supplied directly with battery voltage, not vref.
Vref is mostly used for voltage based sensors.
Thanks for your notice! Indeed this sensor supply voltage should be 8 -> 30V. In elecrical schematics what I have got this is wrong. I will change the supply voltage on Monday and test it again :)
Now it is working well when I connected sensor supply voltage to battery. Thank you for your advices! :)