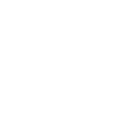
Canbus Termination Issues.
Hi People
A suggestion for evolution of hardware/software to address an issue I have discovered in a specific set of circumstances.
I have a canbus on a MD4 display that has 3 devices on it. 2 are permanently there and the 3rd is a fallback device that may or may not be there depending on circumstances. The 3rd device is a wired remote control and because the wire is an extension of the canbus by its nature it needs to be an end device on the canbus and therefore needs to be properly terminated. If its not on the bus then something else needs to provide termination. I can do that by having a plug in connector that has an epoxied 120Ohm resistor that can be the missing termination when needed, but that is clunky and I really would prefer to not rely on Operators even having to understand what a terminating device is....
If the MD4 display instead of just Yes/No as the choice to terminate the canbus had a couple of alternate options then I possibly could deal with the issue automatically and not require operators to do anything.
One Option would be if the MD4 had an option where we could get it to look at the characteristics of the electrical bus and terminated if it needed terminating. If the MD4 was put on the logical end and an alternate device with termination wired so it extended the bus past the MD4 then such a solution would be electrically correct. If you added the MD4 to the middle of a bus then such a solution would provide correct resistance but would not terminate at the correct location in the bus. So care would still be needed
The second option ( and possibly not a great solution) is to test the potentially unreliable bus to see if a device is present through using a GFIN or J1939Framein to determine if a device is present and then be able to use that to determine if a bus should or shouldn't be terminated programmatically...The issue is of course if the device is present but due to badly terminated bus doesn't respond or isn't heard to respond then.......
Anyway, in my case I believe Option 1 would be a great solution, when the 3rd device is present the MD4 ends up being midbus and when looking at impedance would see the correct 60ohms and not terminate. if it wasn't present the MD4 would be at the end of the bus and would see 120Ohms at the far end and would terminate correctly. The only issue I can forsee is that such an approach cant be a one time check at powerup becuase what happens if its added after the initial check is done.....
Anyone got any thoughts or a different approach that I should take?
Andy
Customer support service by UserEcho
We have the same situation where we have an optional connection that extends the bus and when connected becomes the terminated end of the bus. When the optional connection is disconnected we are needing to terminate the bus at a master module before the optional connection. We are currently trying to use a relay that connects the can bus through a termination resistor when the optional part is disconnected.
The master module CAN bus termination option can be controlled by a digital channel although it has to be an initialization DP only. It may not be feasible, but it would be nice if this could be changed at any point during operation.
Another option would be to use an MC module and enable CAN routing between two ports that are terminated at the master module all of the time. This would allow a terminated break point for your optional connection.