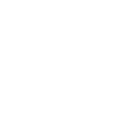
0
Driving PVEM Danfoss With IQAN MC43
Hi folks,
Does anyone here have experience with controlling a Danfoss PVEM valve with IQAN?
Danfoss literature is rather scarce, and I am working with a legacy machine, and trying to upgrade the controllers.
What should the signal be going from the MC43 to the PVEM?
Thanks,
Customer support service by UserEcho
https://webshop.hydrauvision.com/amfile/file/download/file/125/product/1622/
Thanks, I must have missed that in the manual.
Have you successfully used IQAN to drive these valves? I noticed that in the Plus1 forums of Danfoss, folks seem to have trouble driving the PVEM with Danfoss Plus1 software.
Best,
never used these.. wouldnt even, if i seen the 50% to keep the valve in neutral its not a failsave valve... cut the cable and see what happens
I agree, there is no way I would use these either, they are outdated, but I am replacing the controls on this old machine, and I need to understand how they work.
Just to clarify, they appear to have some type of internal failsafe, because cutting the cable will not make them move.
better use the can-bus version.. will safe a lot of IO
Hi Theo, I can't answer your question fully but I may be able to help as I have controlled PVEM actuators with Plus+1 on several occasions even though Danfoss don't called them 'Plus+1 compliant'. You have to be able to drive them with a voltage signal ranging from 25-75% of the valve supply voltage and to do this you have read in what the supply voltage is and adjust your output signal accordingly. This is very easy to do in Plus+1 as they are designed around that.
It is entirely possible the problem people have experienced with PVEM and Plus+1 is that it is a very slow valve and if you are trying to do closed loop control you have to have your gains very low and you will get a very slow to respond system. They also have quite a lot of hysteresis and seem to move the spool in a series of steps rather than smoothly.
Having read some other posts regarding driving the Danfoss PVE actuators with IQAN it sounds like you will run into problems as the IQAN has a minimum current output of 100mA and most PVE including PVEM have high impedence inputs that require a voltage signal not a current signal but you may be able to get around this with a ballast resistor.
Finally, if you cut the wire to a PVEM it will return to its centre position as you have cut the power. I am not sure what happens if you just cut the signal cable - I might test that next time we have one on test in our EMC. It is not unusual to used a DO on your controller that is capable of cutting the supply power to PVE actuators so it can stop uncommanded movements if it can detect them, but also so you can turn the power off when they are not in use to reduce battery gain - for example, if the ignition is on, but the engine isn't running there is no point powering a PVE actuator and running your battery down.
Thanks for the explanation.
One question, you say that I need to drive them with a voltage signal. I understood that it is a PWM?? Are you using that language interchangeably or do I not understand correctly?
Thanks,
Last time we had that issue we concluded that controlling the PVEM with an IQAN-system would require a rather complicated custom made conversion module which raised safety concerns among other things.
We ended up rebuilding the valve with PVHC-modules instead which saved a lot of time and the end result was much better.
If you consider this as an option, I recall that the PVEM and the PVHC required different pilot pressure, so it was not only a matter of swapping the modules, but the pilot pressure valve had to be reconfigured too.
Thanks for all your input, folks, looks like it could be rather sketchy at best.
@Anders Olsson, would you mind sharing more details on what type of conversion module was needed?
Why could logic in MC43 not take care of all the necessary conversion?
Thanks,
Rainer described a conversion module it well in his post!
In our case we were controlling a tree processor which delimbs the trees at 3m/s and cuts them to length with a hydraulically powered chain saw, with the operator just next to it, so safety was our highest concern.
Our machine operators in a very demanding environment, so basically anything can happen to it.
A conversion box between the IQAN and the valve poses a risk in this case, since you lose the valve current monitoring and the extra safety layers that you would have powering the spools directly with the IQAN COUT-outputs.
Both our team and our Parker supplier therefore concluded that, in this case, it was much preferred from a safety point of view with direct current control for the valve spools from the IQAN-module. And the Machinery Directive in our case says that if a foreseeable risk can be reduced by design with simple means and it has now drawbacks on the operation, it is mandatory to do so.
I have already controlled PVEH and PVES controllers with an MC43-FS controller in the past, it works as follows:
Connect a 1K resistor (1W) between PWM out and ground, also connect the pin US of the PVEM control to the PWM output.
With the PVEH and PVES controllers it works with the following parameters:
min MR: 18 Max. MR: 72 PWM frequency: 333 Hz
The control of the PWM out in the programme is then as follows:
0% = P->A; 50% = Neutral; 100% = P->B
I would switch the power supply for the PVEM control via a Dout output which is switched via an emergency off function in the programme (emergency off actuates Dout= off).
I would connect the error pin of the PVEM control to a Din input.
The control works well but the resolution and speed is comparable to the PVED-CC controls.
For this reason, I only use the PVED-CC controllers for new projects.
If you are interested in a IQAN programme to control the PVED-CC controller, please contact me.
Thanks for the information, @Rainer Vermaasen,
Are you suggesting that you would replace the electrical actuators on the valves with PVED-CC to be able to control with IQAN or are you saying that they are similar enough that the IQAN logic for the PVED-CC should work for the PVEM? Have you been able to try your logic on the PVEM if that is the case?
Thanks,
@ I Can Go
You have to make a fundamental distinction:
The PVEM and PVEH / PVES controllers are controlled via an analogue voltage signal.
The PVED-CC controller is controlled via CAN bus.
In your application, it is possible to control the existing PVEM controllers with an MC43 control unit using the programme logic described in the last article.