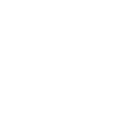
0
Answered
why PWM instead of COUT?
I am planning to drive a proportional relief valve (AP04G2YR 21C) with a XA2.
Is there any reason to use a PWM output over a COUT?
With COUT, I would think I would have open and short circuit detection (not sure about PWM) and it would take into account the coil heating up over time.
Customer support service by UserEcho
When driving proportional solenoid it is adviced always use the COUT. The COUT channels use pwm modulation with current control to control the demanded current. The commanded mA current through the solenoid gives an proportional pressure or displacement (spool in flow valves) of the valve. COUT current control also compensated for changes in coil resistence (by temperature) and supply voltage, so getting best performance out of the valves. The Min and Max current can be set more accurate compensating deadband and limiting current to maximum recuired level.
The pwm in the COUT acts as dither reducing hysteres of the valve, the pwm setting can by adjusted and optimised to valve requirements.
As you mentioned COUT has also cirquit fault detections for easy diagnostics and safe operation.
The literature for the valve https://www.parker.com/literature/Literature%20Files/IHD/PDFs_060908/VIN_Proportional_Valve_AP04G2YR_21Cseries.pdf
makes it sound like they want PWM control, but as you said; COUT is basically just monitored PWM.
When should I use the IQAN's PWM? Lights and fans under 2 amp? When giving a signal to another system?
As Jos explained, the IQAN COUT channel is a PWM output with closed loop current control where the command is given in mA, and the output automatically adjusts the modulation ratio to compensate for variations in coil resistance and supply voltage.
The IQAN COUT should be your default choice whenever there are performance requirements on having a repeatable result.
One reason for configuring the output for open control PWM instead is if you need to drive a current that is too far below the COUT operational range. On the IQAN-XA2, the COUT controllable range is 100-2000 mA, if you attempt driving a lower current the regulator cannot control the current, and the error detection stops the output.
Say that you will not need to control it below the 19% level, with a 19 W 24 V Supercoil, you get 580mA*19%=110mA as the min current, so using a COUT as recommended should be fine.
If you needed to go much lower than 100 mA, then open control PWM could be the way to achieve it.
Other reasons for selecting open control PWM instead of COUT:
Another reason for choosing the open control PWM in general is if you are running out of COUT:s.
On the IQAN-XA2, the exact same pins combinations are used for both COUT and the open control PWM.
But on for example the IQAN-MC43, there are additional outputs that provide open control PWM, these could be used for functions with lower performance requirements.
Finally, on the XA2, MC2 and TOC2, the proportional outputs should be configured for open control PWM when driving the classic 33Hz and 75Hz Parker pulsar valves. On XA2, MC2 and TOC2, the internal diode for the COUT is disconnected in PWM mode, giving a more aggressive dither needed to avoid hysteresis in the 33Hz and 75Hz pulsar valve. Some more info here. It is worth noting that for loads larger than the pulsar coils, external clamping diodes should be added when configuring these outputs for open control PWM!
Thanks for the in-depth explanation.
Hi...i am a new user here. As per my knowledge the reason for configuring the output for open control PWM instead is if
you need to drive a current that is too far below the COUT operational range. On the IQAN-XA2, the COUT controllable range is 100-2000 mA.
"Finally, on the XA2, MC2 and TOC2, the proportional outputs should be configured for open control PWM when driving the classic 33Hz and 75Hz Parker pulsar valves. On XA2, MC2 and TOC2, the internal diode for the COUT is disconnected in PWM mode, giving a more aggressive dither needed to avoid hysteresis in the 33Hz and 75Hz pulsar valve. Some more info here. It is worth noting that for loads larger than the pulsar coils, external clamping diodes should be added when configuring these outputs for open control PWM!
With IQAN-MC3 and IQAN-MC43, -MC42 and -MC41, the internal clamping diode is not disconnected when COUT pins are used as open control PWM. That is why we advise against using these modules to drive the 33 and 75Hz pulsar coils."
After reading this, I'm still not fully understanding why the 33hz and 75 hz pulsar valves can't be driven with a current regulated output. Why does using open control provide a more aggressive dither? Why do the Pulsar valves need a more aggressive dither? Are they not manufactured to close tolerances?
Could this be elaborated on?
Hello Barnhart,
The Pulsar valve has a very low mass operating stage and fully opens and closes for each PWM cycle. This means the valve fully opens and closes at 33Hz or 75 Hz. The Pulsar control wave form has to be square in order to get the valve to travel to and from end stroke. The diode in the COUT drivers would take the edge off the square wave form and make the Pulsar difficult to control. The purpose of PWM in the case of the Pulsar is to fully open and close the valve rather create dither/mechanical excitation.
Kind regards,
Nick.
Hello The Parker Pulsar is fast switching on-off valve, see working principle in VPL series Parker Mobile Valves catalogs. That's why it needs square PWM to operatie well.
Page 8
Thanks for the detailed feedback.
Do Pulsar valves still have decent repeatability despite using open control? Do they sacrifice having good proportionality by being digital?
Hello. There are various Pulsar solenoids to pick from now. The 33 Hz and 75 Hz Pulsars are only digital solenoid valves. This means that they shift at full stroke, open to pilot pressure, then shift back at zero stroke, open to tank pressure, 33 or 75 times per second. This "on/off" digital control give these solenoid pilot valves a very low hysteresis when driven open loop. Since they turn 'on' and 'off' to full stroke over a controlled time interval, they are repeatable. However, high viscosity fluid (300+ Cst) will affect the response time, making it less repeatable when the fluid is cold.
The coil has a low inductance for fast response 'on' time (~1 ms). The coils have a relatively low current draw so that they are not as sensitive to rising coil temperature, compared to many other traditional coils. The Pulsar solenoid requires a negative spike when turned 'off', to collapse the magnetic field quickly. A zener diode (or equivalent) is should be used with the open loop PWM output to give very good control. If a clamping diode is used, the proportional control is not very good. If the solenoid is connected to the COUT driver, then the solenoid behave as an on/off solenoid (no proportionality).
The 33 Hz Pulsar was launched in the late 80's and the 75 Hz Pulsar in the early 2000's. Then about 2015, a new Pulsar solenoid was launched that could be driven with either PWM or COUT drivers. This Pulsar is referred to as a "Pf" solenoid valve, for "pressure feedback". This solenoid acts like most other 'pressure reducing' solenoid valves where the electro-magnetic force on the pilot spool increase as the current applied increases, and the resulting output control pressure then acts on the opposite end of the spool to provide a 'feedback' force against the solenoid force, which then produces a steady state balance, for a very repeatable output. Therefore, the pressure output is a function of the current input. Even if this solenoid is driven with a PWM signal, the solenoid is still acting to reduce the pilot pressure.
If the Pf Pulsar is driven with an open loop PWM output, the recommended frequency is still 75 Hz. This allows for this Pf solenoid to be used in place of the older 75 Hz digital Pulsar, for any new applications. The cost for any of these three Pulsar models are the same. Note that the pilot pressure for the Pf Pulsar should be set to 210 psi, whereas the pilot pressure normally used with the 75 Hz Pulsar was set at 150 psi.
If the Pf Pulsar is driven with an closed loop COUT output, the factory recommended frequency is 90 Hz. When the solenoid is current controlled, the driver does not require a negative spike, so a normal clamping diode can be used. Also, the spool excitation is less, so the hysteresis will be more than what is normally obtained with the PWM signal. However, the frequency can be tried at a lower value to improve the hysteresis, while monitoring the stability of all the machine functions. With some controllers, the dither amplitude can also be increased to find the optimum performance of hysteresis and stability.