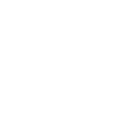
0
Answered
Hatz Engine CAN Throttle Issues
Hello,
My Customer is using a Hatz 4H50TIC diesel engine.
For this project, we are to throttle the engine using Can.
I have imported the pre-configured TSC1 Can solution. I changed nothing from the default settings/
So far, i show to be sending my command but the engine will not respond to anything no matter the settings. i cannot find anything from Hatz about TSC1 commands. If anyone has experience with can throttle on Hatz engines and has advice, that would be extremely helpful
Customer support service by UserEcho
Probably not very helpful but we had one engine manufacturer state that the IQAN TSC1 block wasn't 'proper' for throttle control so we had to write one.TSC1.idex . I cannot remember what they said was wrong with it.
mdonaldson,
Thanks, looking at your application I can see that it has the TSC1 control purpose set to 2, meaning PTO governor.
The built in TSC1 channel has the bits for control purpose on the original setting (all ones), which means temporary powertrain control. But up until now, I have not come across this as an issue.
Sorry I made it should like I was implying something is wrong witht he TSC1 function. We have had no problems with it. When this manufacturer stated it didn't work we took it with a huge grain of salt.
Hey Mike. While i do find the breakdown itself helpful, i wouldnt know what the values would need to be for Hatz to recognize it. I have sent a message to Hatz to see if i can get that info, but have had no response yet. Thank you MIke!
In my experience, issues with sending TSC1 tend to be one of the following:
1. The source address of the controlling device. Your IQAN master has SA 39 as default, depending on the engine controller and the application, this may need to be changed. Common values that engine controller accept are 17 (cruise control), 33 (body controller), 39 (management computer). The source address 3 for transmission controller is also common, but of course this shouldn't be used unless you use the IQAN module as the transmission controller.
2. Transmit rate. Default setting in your IQAN application will be to send with the application cycle time, while most engine controllers require 10 ms for TSC1, at least when sending speed control. If your cycle time isn't 10 ms, you should change the Transmit rate property for the TSC1 channel to 10 ms.
3. More recently, some engine controllers requires TSC1 checksum/counter. Then this property on the TSC1 channel needs to be turned on.
Of course, this all assumes that you have an interface to the engine that supports TSC1.
Gustav,
Thank you for the wisdom! This will most certainly come in handy for future speed control applications.
A solution was found for my issue. Hatz will probably work with the TSC1 imported solution, however you will need to set your J1939 source address in the TSC1 block to 3. In my experience, the transmission, which is always address 3, doesnt send PGN 0 so it was a little odd to me. You dont need to worry about counter or checksum either. This info came from a Hatz engineer so i hope this may help anyone with CAN speed control for Hatz engines.