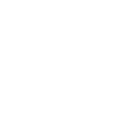
0
Driving PVEM Danfoss With IQAN MC43
Hi folks,
Does anyone here have experience with controlling a Danfoss PVEM valve with IQAN?
Danfoss literature is rather scarce, and I am working with a legacy machine, and trying to upgrade the controllers.
What should the signal be going from the MC43 to the PVEM?
Thanks,
Customer support service by UserEcho
https://webshop.hydrauvision.com/amfile/file/download/file/125/product/1622/
Thanks, I must have missed that in the manual.
Have you successfully used IQAN to drive these valves? I noticed that in the Plus1 forums of Danfoss, folks seem to have trouble driving the PVEM with Danfoss Plus1 software.
Best,
never used these.. wouldnt even, if i seen the 50% to keep the valve in neutral its not a failsave valve... cut the cable and see what happens
I agree, there is no way I would use these either, they are outdated, but I am replacing the controls on this old machine, and I need to understand how they work.
Just to clarify, they appear to have some type of internal failsafe, because cutting the cable will not make them move.
better use the can-bus version.. will safe a lot of IO
Hi Theo, I can't answer your question fully but I may be able to help as I have controlled PVEM actuators with Plus+1 on several occasions even though Danfoss don't called them 'Plus+1 compliant'. You have to be able to drive them with a voltage signal ranging from 25-75% of the valve supply voltage and to do this you have read in what the supply voltage is and adjust your output signal accordingly. This is very easy to do in Plus+1 as they are designed around that.
It is entirely possible the problem people have experienced with PVEM and Plus+1 is that it is a very slow valve and if you are trying to do closed loop control you have to have your gains very low and you will get a very slow to respond system. They also have quite a lot of hysteresis and seem to move the spool in a series of steps rather than smoothly.
Having read some other posts regarding driving the Danfoss PVE actuators with IQAN it sounds like you will run into problems as the IQAN has a minimum current output of 100mA and most PVE including PVEM have high impedence inputs that require a voltage signal not a current signal but you may be able to get around this with a ballast resistor.
Finally, if you cut the wire to a PVEM it will return to its centre position as you have cut the power. I am not sure what happens if you just cut the signal cable - I might test that next time we have one on test in our EMC. It is not unusual to used a DO on your controller that is capable of cutting the supply power to PVE actuators so it can stop uncommanded movements if it can detect them, but also so you can turn the power off when they are not in use to reduce battery gain - for example, if the ignition is on, but the engine isn't running there is no point powering a PVE actuator and running your battery down.
Thanks for the explanation.
One question, you say that I need to drive them with a voltage signal. I understood that it is a PWM?? Are you using that language interchangeably or do I not understand correctly?
Thanks,