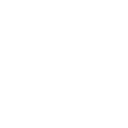
0
XA2 No contact error. The led indiactions are fine. All XA2 after this module has status OK.
Jacob Mathai 5 years ago
in Expansion modules / XA2, XS2
•
updated by Gustav Widén (System support) 3 years ago •
4
XA2 No contact error. The led indications on the XA2 module are fine. All XA2 modules after this module on the expansion bus has status OK. Could Anyone point out what is going on here Please?
Customer support service by UserEcho
Hi Jacob, if it is one XA2 on the bus, then it could be a few things. First, is the power supply different for this particular XA2? If it is 12 VDC and the others are 24 VDC, then maybe the power supply is drooping at startup causing the issue? If the wrong ID tag is installed, the master module would not recognize it.
Hi Kerry, thanks for the reply. There are 4 expansion modules in this bus. This particular XA2 is in the second position. Intermittently XA2 module no contact error appears. I replaced the module, the fault did not go away. The green led light is solid and the yellow led is blinking as it should. All other Expansion modules in this bus are fine. After cycling power to the machine the fault goes away and does not come back for 4-5 hours. I checked the address tag, it is intact. What might be the issue here?
Hi Jacob,
The fact that it works for awhile after cycling power is telling. I'm thinking you could either have incorrect bus termination, electrical noise, or the stub to this module is intermittent.
Not sure if you are using internal termination. I prefer not to, and always use external termination resistors (120 ohm - 1/2W), as it allows me to physically validate the number of termination resistors as well as where they are installed, without needing to look inside the application. If using internal termination you will need to go into the app to check these settings.
There should be one termination resistor located at the each end of the CAN bus. A missing terminator, or more than two, can cause problems like you've described. I haven't checked a bus when using the internal terminators, but know that if you use a digital voltmeter to check resistance of a CAN bus, it should measure around 60 ohms, with the system under test powered off. If it measures 120 ohms, you have a (one) missing terminator. If it's significantly higher than 120 ohms, you have two missing terminators. If it measures around 45 ohms, or less you have too many terminators.
The only other possibilities I can think of is if the CAN bus is routed along with the power leads. When large currents are switched on/off, they can induce noise on a CAN bus, which in turn will cause an affected IQAN module to Bus Off. I've actually seen this on a vehicle which had a 24V air compressor, which was causing multiple modules to bus off, as the CAN wiring was in the same harness as the power wiring going to this compressor. You might look at the application using the Measure function when this happens to see what errors are shown internally by the module, if any.
Th last possibility I can think of is an intermittent CAN bus wiring stub connecting this module to the main bus.
Good Luck. Finding out the "why" of an intermittent can be hard.
Mark
Thanks for the clear explanation Mark.