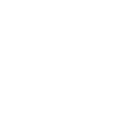
0
COUT configuration for Danfoss PVHC
Does anyone have experience with programming a Danfoss PVG with PVHC 12V coils? I'm trying to configure with COUTs and PWMs with an MC42 but I keep getting an open load error. Trying to get joysticks to control the current output and I am getting a very small mA reading
Customer support service by UserEcho
We had to throw a resistor in parallel
https://forum.iqan.se/communities/1/topics/1622-xc10-pwm-out-overload-danfoss-pvea
Thank you, we will give that a try. Did you end up sticking with the PWM output, instead of a COUT?
We did, then they quickly moved to a CAN controlled valve.
We might end up replacing it with the L90 instead lol
I would definately recommend an L90 valve.
Hi Deanne,
Definitely recommend L90LS for your directional valve needs.
Use COUT to drive L90LS and Danfoss PVHC. I don't recommend you use PWM, the PWM output channel is primarily used to control Parker pulsar valves.
Danfoss PVHC is not the same as PVEA. PVHC utilises Thomas Magnete proportional solenoid valves in a similar way to L90LS and therefore should not require any resistor. The PVHC will run nicely from an IQAN COUT.
This is from the Danfoss PVHC datasheet, so you could start with 560mA Minimum current and 1000mA Maximum current:
Regarding the open load error, I suspect you have a wiring problem. Check that you have the high side output connected to both coils, make sure you have the valve connected like this:
Thanks so much for your insight Tim.
Would you happen to know why I might be getting a reading of less than an amp when a meter is hooked up? For this instance, I have one COUT for pins 14, 39 and 55. We are reading from just 14 and 39 and I wonder if that is why. I followed a similar DMAC format to the one you had posted previously.
Hi Deanne,
If you want to know the current flow to the valve, I would recommend setting up a measure group within your project for the COUT channel and then use IQANrun or IQANgo or even IQANdesign to measure the value in real time without causing any disturbance to the connection of the valve.
If you really want to measure the current with an Ampere meter (not recommended) then you should be in series between pin 14 and the load. Please remember if you are working with the current output wires you must have the system powered down. A sudden voltage spike generated by field collapse of the inductive load if the supply current is interrupted - will damage the output permanently.
Hi Tim,
We were able to get it working now - thank you very much for your help.
Just to add on on a slightly different subject, why is it not recomended to use PWM for an L90 valve section?
If I would use it, how would I configure it?
Here is a post regarding PWM vs COUT: https://forum.iqan.se/communities/5/topics/686-why-pwm-instead-of-cout