
MC41 Settings Overflow
I am receiving this settings overflow message via (1 long amber flash, followed my 4 short amber flashes). Any idea as to what could be causing this?
This is a different error than calculation overflow, which I am familiar with.
Thank you for the help!
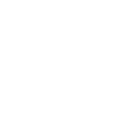
Blue screen on MD4-7 while operating
Hi,
I was wondering if anyone had blue screens happening while in operation?
I currently have an intermittent blue screen problem on an Md4-7 running Iqan 6.06. Images of one event are attached. The busload on the can-buses are low with no error frames.

Problem exporting languages to Excel
When I export languages I get a 34kB .xlsx file
If I open it with Excel 2019 I get a message asking if it should try to repair a damaged file
"Vi hittade ett problem med visst innehåll i "språk test.xlsx". Vill du försöka återskapa så mycket som det går?"
If I select yes it opens a workbook that has four sheets but there is no data on any of the sheets.
Complete error message in Swedish after clicking "Edit":
"Filnivåvalideringen och reparationen har slutförts. Vissa delar i arbetsboken kan ha reparerats eller tagits bort. Borttagen del: /xl/sharedStrings.xml-del med XML-fel. (Strängar) Ogiltigt xml-tecken. Rad 431, kolumn 49.
Borttagna poster: Cellinformation från /xl/worksheets/sheet1.xml-del Borttagna poster: Cellinformation från /xl/worksheets/sheet2.xml-del
Borttagna poster: Cellinformation från /xl/worksheets/sheet3.xml-del Borttagna poster: Cellinformation från /xl/worksheets/sheet4.xml-del"
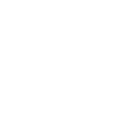
System Software Push
We are getting ready to launch a product using IQAN Software. As we make major changes, how can we push them into the field? Without the customer needing to do a lot of work?
We have a MC43FS and MD4
Thank you
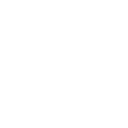
Set Date/Time from IQANDesign Code
Hello,
It would be nice if we could set the date/time automatically through the IQANDesign application. We have a way of getting the current date/time from an external module, there's just no way as far as I know to force the application to sync with that time.
So I imagine it could look something like this
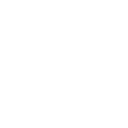
Redundant CANBus utilization
Some components have redundant CANBus inputs. IQAN can use these by having multiple CAN outputs assigned to different CANbus. It would be nice to have a built in function that could swap an output to a different bus automatically on bus failure or using a logic input.
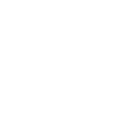
Ambiguous module address
In a program, I always used multiple expansion modules with the same address with no problem.
this to select for different output setups (COUT instead of DOUT and so). via a setting one of the modules was enabled.
physically there is only 1 module but by enabling one or the other in the program is was possible to switch between the different setups
in Design 6.x this not possible anymore because it generates an Ambiguous address error.
any suggestion the deal with this
regards Ed
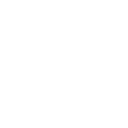
COUT Disable Bug?
IQANdesign 6.04.9.5943
MD4-7 & XC43
I just diagnosed what I think is a bug for the current outputs. I have a COUT going to the max positive value, then while the COUT is at max, the channel gets disabled. When the channel is enabled again it turns on by itself at the previous value where it was disabled at. The length of time it stays at the previous value is affected by the ramp settings.
In my opinion the COUT should zero itself when disabled since that is the safe state.
Customer support service by UserEcho