
LC5 query
Are there any example programs for the LC5 joystick?
Currently utilizing the 2007699 (lc5-c01-mpb2w2t1) joystick
using iqan design 6.02. I get the LC5 and link it to an MC43 on system layout but how do i get the axis outputs and button digital io? I can find no EDS file or instructions as to PDOs for the outputs?
Thanks in advance
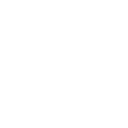
Impicit value type conversion
Since version 7 I get a "Impicit value type conversion" warning when I use a Derivative function in the activation part of a value log item.
Does anyone have a idea how to solve this?
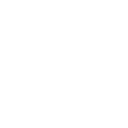
IDC Delay on / off time limit
Why is the IDC delay on / off time [ms] limited at 3276750 in version 7
(and unlimited in version 6)
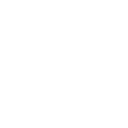
XC43 PWM out HS+LS internal free wheeling diode
We are swapping out from the XA2 to the XC43 and we originally thought we were going to be using the PWM HS output so we attached a ark suppressing diode on the 4-way 3-pos cart valve (HSP 10-47CB-0-v-24ER). We however ended up using the PWM HS-LS output which has a internal free wheeling diode. Is the newly installed ark suppression diode going to case problems down the road. and is it best practice to just use the internal diode on the PWM HS+LS output?
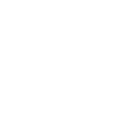
IQAN D6 Corporate licence expires soon
Hello, our corporate D6 licence expires 11/06/2023. if we do not renew, what is the impact to our users? We do not want to go to version D7 just yet. We want to make sure that we can still use the current version. Please advise.
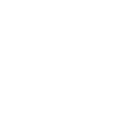
Issue with JFOUT sending to a DA
I am having an issue in IQANdesign 7.00 when I set the destination address in a JFOUT channel to either "Assigned Module" or the actual SA number. I get a "No Contact" message. When I use IQANanalyze I can see the CAN frames from both the IQAN master (MC43) and the third party device. If I set the destination address to a value not used by any other module on the bus, I no longer get the "No Contact" error and I can read the CAN messages sent from the third party module. The CAN structure of the message is a little odd to me, as messages from both the IQAN master and the third party module use the same PGN number, 61184 to send information between the two modules. This structure is part of the CAN protocol used by the third party device. I cannot figure out a way to send a CAN frame (JFOUT) to a specific SA without getting the "No Contact" error. I even tried changing the "J1939 source address" line in the JFOUT to 39 instead of "Default" and it did not seem to affect the "No Contact" error.

qcode MAC channel - MinOf multiple if else statements
How to run MinOf function within MAC channel using qcode if multiple if else statements are used?
Example:
[1] If ......... else .....
[2] If ......... else .....
[3] If ......... else .....
[4] If ......... else .....
[5] If ......... else .....
[6] If ......... else .....
MinOf ([1],[2],[3],[4],[5],[6])
Is this possible with qcode using just one MAC channel?
Thank you
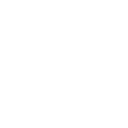
Difficulty sending programs to new MD4s running 6.08.28
I'm frequently seeing issues sending programs to brand new MD4s which are running firmware 6.08.28. The main issue I'm seeing is messages saying no reply from master module. Yesterday I had one brand new module where I tried sending a blank project from iQAN design 6.08.30 several times before it went in.
We only ever send projects to the modules over a direct ethernet connection. This is occurring with different cables and even when sending projects using iQAN run. Is this a known issue?

Multimaster No contact error with external module connected to both master but works
Hi,
I'm using two MC43 that are both linked to a remote controle(generic) by canbus B.
I have a display on my remote and I can send information through 4 RPDO to show data on the remote screen.
It's working well from my master MC43[0], but when I send my canbus messages from the MC43[1] I have a "no contact" error message that appear BUT the crazy thing is, I still receive my data on my screen !
I see the data on the screen and I see it also with PCAN-View :
So the data is sent, but my master think there is no contact.
I had the same problem before with my both MC43 calculators and a MD4-7 that was in the project.
I had some touch buttons on my MD4-7 screen and when I sent the data from MD4-7 to masters, It was OK with MC43[0] but no contact with the MC43[1], BUT I still receive the data.
Is there something wrong on my multimaster system ?
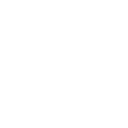
Alien Module Detected
Hello,
When I view my IQAN project in IQANRun I see that the master module is reporting Alien Module Detected.
I have two IQAN projects.
Project A is a multi master project with a MD4-7 (ID tag 0) and MC43FS (ID Tag 1).
Project B has a single MC41FS (ID Tag 7)
The other CAN ports on all these controllers are connected to a number of different devices.
All controllers CAN A are connected together. In IQANDesign CAN A is setup as the DIAG bus and for J1939 traffic. The master module communicate with each other via J1939 PGNs.
Everything appears to be working properly except I see this message about alien module detected. I assumed since these are two separate projects and all master controllers have different ID tags they should not care.
Is this a bug? Design issue?
Another issue is that when uploading Project A is causes Project B controller to also enter a programming state even though it will not be programmed. Is there not a check that is done by the controllers to see if they are a target that is going to be programmed? Is this another bug?
I am using IQANDesign 7.
Customer support service by UserEcho