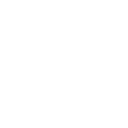
MC43 RAM Utilized
We just wrote our first program an MC43 and it is taking up 1.4 of the 1.5MB.
I thought the days of watching RAM utilization was gone after the MD4 came out.
Our last 2 programs utilized the MD4 as the master.
Will IQAN 5 help with decreasing RAM utilization or what is the best practice to try to reduce it in this program?
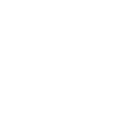
From version 4.0, I miss the XT2 at the modules
From version 4.0, I miss the XT2 at the modules

XC21 Status
When using the XC21 Module Diagnostic "Status" the Help indicates that there fault codes - is there a list of these fault codes that I can use?
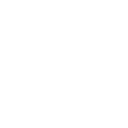
G11 bluetooth Sensors
Is the G11 capable of reciving Bluetooth signals from a bluetooth sensor to be displayed the screen?
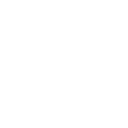
External Button Control Issue
If I have a button in a group and try to use an external control. The control outline is use the group left and top values (which are 0,0) instead of the actual left and top values.
This is trying to select button 2.
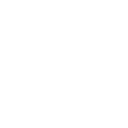
Full list of mdgn status values
Is there a full list of Status Values for the module diagnostics? Given values are no contact=203 and ok=64. I'm displaying a message if the sensor triggers (looses power), but when the XA2 has no contact or other error it will falsely display causing confusion with the customer. I'm intending to block the error for no contact, critical can, address, etc. but not for output, input, vref, temp, etc.
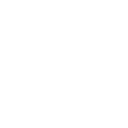
Load Moment Indicator System
I found this Bulletin LMI HY33-5054_US and I like to know how can i do this program Because this bulletin says someting about boom length sensors. But I can´t find information about this sensors or how can I measure length of the crane booms?
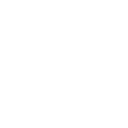
MD3 System Memory High Alarm
We are getting a system alarm for high memory on an MD3 Display. 2 questions
1. What are the thresholds for this alarm ? We are close but below the specifications (according to the statistics, see photo)
2. If we determine our application is functioning properly is there a method to remove this alarm, at least from displaying on the screen. Keeping it in the system log would be fine.
Thanks,
Mike
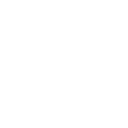
MC4x PWM Frequency
Is there a reason the new MC4x family doesn't support PWM frequencys in the 10-70Hz range? I know the XC10 will go do to 10hz and the MC31 went down to 25.
I have an application the MC42 would be perfect for, but I need one output at 32hz and another at 50hz.

J1939 DM1 Channel
We are currently doing a control system for a new track drive machine. The engine that is being used is a Tier 4 Final unit. The manual that comes from the manufacturer is asking for an extensive library of DM1's but I do not understand the format that they are using to present the information, and how we use their information to format the DM1 in Iqan design. Additionally they are asking for ISO symbols to be used on the display that do not appear exactly like this in the library - eg ISO9000-2945 but with an exclamation mark on top of it - do you have any additional symbols available?
The Information that they are giving for the message identifier is like this :-
Byte 3 2 1 0
Message 18 FD B4 3D
Start Position Length Parameter Name SPN
1 2 bytes Aftertreatment 1 Exhaust Temperature 1 3241
Byte 3 2 1 0
Message 18 FF 28 3D
Start Position Length Parameter Name SPN
1 1 bytes Dosing Module Status N/A
2 2 bytes Actual reducing agent quantity N/A
I wonder if you might be able to help me to understand how to configure the DM1 channel in iqan design?
Customer support service by UserEcho