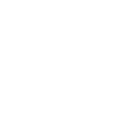
How do I create a generic j1939 application?
I am new to using IQAN Design and I have a J1939 CAN bus application that I need to create.
Basically I have two buttons that will control a J1939 linear actuator. When I press one button the actuator should retract and the other button extends the linear actuator. Each actuator is controlled over a CAN bus with a specific J1939 protocol that I will have to configure manually. I need some help getting started with this application. Thanks...

Parker IQAN-LM Plug&play Joystick Replacement Kit
Hi!
SGI Group, in partnership with the Parker-Hannifin engineering team, has developed a solution for replacing Parker IQAN-LM joysticks worldwide.
This solution comes in a Plug&Play replacement kit. In mere minutes, your new joystick will be operating with 100% of the electronic features of the old one. Just simply place the components and connect them with the characteristic green connectors.
The solution comes in two versions so that you can choose the kit that best suits your needs.
https://www.sgingenieria.es/en/parker-iqan-lm-kit-solution/
SGI Group, en colaboración con el equipo de ingeniería de Parker Hannifin, ha desarrollado la solución de reemplazo para joysticks de la familia Parker IQAN LM . Es un kit de sustitución Plug&Play. En pocos minutos su nuevo joystick operará con el 100% de la funcionalidad electrónica del anterior. Simplemente precisa la ubicación de los componentes y el conexionado de sus característicos conectores verdes.
Esta solución se presenta en doble versión, pudiendo adquirir el kit que mejor se adapte a sus necesidades.
KIT_PLUG&PLAY_REPL_JOYSTICK_PARKER_IQAN_LM.pdf

Can I influence the lamp status of DM1 Out?
Can I influence the lamp status of the DM1 Out message? So the status of the four lamps. I understand that the Amber Warning Lamp is activated when there is at least 1 SPN active. But what about the other lamps?
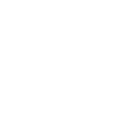
log csv export timestamp
I seen different kinds of timestamps in CSV log files retrieved from the MD4-7
We use the retrieved csv log file as an input data to our reporting application and have had problems when try to import the csv file because the timestamp is in another format
1. Have the timestamp changed between the program versions
2. What is affecting the timestamp(language?) and can it be forced to certain type?
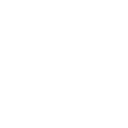
Simulink Model in IQAN MD4-7 Module
Hello,
Is it possible to load in compiled simulink models into IQANdesign configured to flash onto an MD4-7 module? Thanks.

CAN routing with modifications
Hi all,
Is there a simple way to do CAN routing from one channel to another using the CAN routing option where we block one incoming PGN on the. IN BUS, then with a JIFIN etc, read the same PGN coming in, and modify 1 BYTE and send it to the OUT BUS with a JIFOUT. Rather than adding every PGN to and passing them through etc?
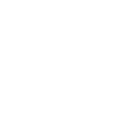
IQANdesign 7 not able to program using Bluetooth
Hello, I just updated from Version 6 to Version 7 and cannot send or receive programs through Bluetooth.
Setup:
Modules: MC43 / G12.
IQAN Design Version: 7.00.45
Issue:
Using IQAN Design through Bluetooth, I can connect to the G12 and see the diagnostics when selecting start measure. But it will freeze when selecting stop measure.
After attempting to select Send or Received, IQAN Design goes to "not responding" and freezes.
It does the same when trying to update the "Set Date and Time" only through IQAN design.
We have 2 other team members with the same issues.
I have no issues using Version 6.
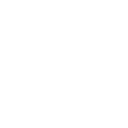
Iqanrun6 and 7 Password request to upload new project file
trying to upload a parameter change file from factory to a module. I click send file using version 7 or new project using version 6. Both prompt for password as soon as I select file. I have another technician using same process and no prompt for password. There shouldn't be a password.

IQANrun license/internet issue
I am failing to Connect to IQANconnect Server when trying to connect to remote. I have full internet access and can browse web pages correctly, but it appears the license cannot pull correctly. Internet Connection is working and no proxy is required.
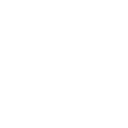
IQANgo 7.00 for Android fails to connect via internet
We are using iqan connect for quite some years already.
But yesterday we got the update on our android devices to iqango 7.00.38
we connect remotely to G11 modems with firmware 1.12.2.1722.
So far that works, but for some reason a connection to the MC43 master is not possible which has a project built with IQAN design 6.08.22.8040 (older versions also don't seem to work).
This worked perfectly before we got the update, unfortunaly we cannot undo the update as our phones all updated themselfs.
We are in the middle of harvest and already had a dozen of customers which we cannot help properly because we cannot login to their machines.
The connection over bluetooth over iqango or iqan design without iqan connect in between works like it always did, but the remote connection just doesn't.
the message as can be seen below shows up for ourselfs, and that's it.
Customer support service by UserEcho