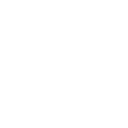
XA2 DOUT problem
I have encountered a problem with DOUT on XA2 modules. We operate several Parker D1VW (NG6) valve, with multiple XA2 modules. Some DOUT (from different XA2) does not activate the magnet coil, although it looks completely correct when I'm connected to IQAN Design . DOUT = Tru.
We use valve contacts with zener diodes, it works on most DOUT otherwise. I had to change the output to PWM instead and then it works without a problem. Is there any problem with the XA2 modules, or are the Zener diodes that do not work against XA2?
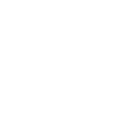
xa2 voltage drop
Due to a voltage drop in the system, because of an electric fan switching on, all the voltage inputs give a low error.
The strange thing is that the voltage drop is not so big. it drops from 27 to 22 for only a sec due to the high start current of the fan.
Is this normal, I thought the modules could be used in 12 VDC system also. So the voltage drop should not be a problem.
regards,
Ed
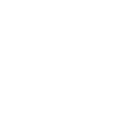
XC23 Can Error Flash Disabling Module?
We have a system with MD4 connected by master bus to MC3. We have a XC23 connected to the MC3 via expansion on different bus to master.
On ignition switch on the system appears fine and all outputs and inputs into XC23 are OK, during engine start there appears to be a dip in voltage which causes the XC23 module to show 3 red, 1 amber LED flash (can error / timeout). When we get this error flash, IQAN run says system health is OK under the XC23 and MC3 modules and IQAN design shows the outputs on XC23 going true and false as expected. XC23 module outputs however are non functional, the module is in error state and refusing to operate outputs whilst the LED flash sequence above is active.
There are no logs in the MC3 for failed communication with XC23.
Are there any recommendations for how to resolve this? Is this normal behaviour for a dip in voltage on XC23? All other modules appear to be unaffected by voltage dip, its almost as if XC23 does not recover and outputs are non functional even though IQAN design thinks they are? Would pulsing 'enable' property just after engine start re-enable the module in event of this error flash?
Running IQAN Design 4.07 with machine voltage 24V dipping to around 10/12V on startup.
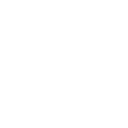
Multiple XC10s No Contact or Multiple Addresses Intermittent Issues
We are having issues with a system that has 2 XC10's on the same expansion bus. This is the first system we used multiple XC10's and have been having issues since we got it online.The XC10's expansion bus is connected to a MC43.
Changing different settings seems to have some affect but I feel like no matter how we change settings this issue is still around it just might not popup as much.
We either get a multiple address error or a no contact error. When we get the no contact error if we look online the device is working however any outputs that were active are faulted and we need to cycle them to get it going. This seems normal for a no contact issue. We see these errors on startup and occasionally while running.
Here are settings I changed. When I changed them I cycle power 25 times to try to gauge where we need things set. The settings I played with are the MC43 cycle time, expansion bus divider, delaying and staggering the 'Enable' for the XC10's. And I recorded the occurrences of each message.
There is a pattern but I'm having a hard time decided where to set things. We currently have the system set with settings that didn't give us problems during the test, but during further testing we occasional see them.
20 ms MC43
Expansion bus divider = 2(40mS)
Cycle util = 11%
XC10[0] Enable delay = 0000
XC10[1] Enable delay = 0000
0 - No Contacts
0 - XC10 Multiple addresses
10 ms MC43
Expansion bus divider = 2(20mS)
cycle util = 21%
XC10[0] Enable delay = 0000
XC10[1] Enable delay = 0000
0 - No Contacts
2 - XC10 -Multiple addresses
10 ms MC43
Expansion bus divider = 2(20mS)
cycle util = 21%
XC10[0] Enable delay = 5000
XC10[1] Enable delay = 0000
0 - No Contacts
2 - XC10 -Multiple addresses
10 ms MC43
Expansion bus divider = 9(90mS)
cycle util = 21%
XC10[0] Enable delay = 0000
XC10[1] Enable delay = 0000
0 - No Contacts
0 - XC10 -Multiple addresses
5 ms MC43
Expansion bus divider = 2(10mS)
cycle util = 41%
XC10[0] Enable delay = 0000
XC10[1] Enable delay = 0000
0 - No Contacts
4 - XC10 -Multiple addresses
5 ms MC43
Expansion bus divider = 2(10mS)
cycle util = 41%
XC10[0] Enable delay = 5000
XC10[1] Enable delay = 0000
0 - No Contacts
3 - XC10 -Multiple addresses
5 ms MC43
Expansion bus divider = 10(50mS) ,
cycle util = 41%
XC10[0] Enable delay = 0000
XC10[1] Enable delay = 0000
1(1) - No Contacts
0 - XC10 -Multiple addresses
5 ms MC43
Expansion bus divider = 10(50mS)
cycle util = 41%
XC10[0] Enable delay = 4000
XC10[1] Enable delay = 8000
1(1) - No Contacts
0 - XC10 -Multiple addresses
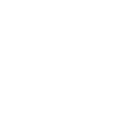
XA2 power off D-in impedance
I have D-in G, pin #38 hooked up to the brake lights of a truck to detect when the brakes are on.
I recieved a report on one truck that the brake lights don't work when the IQAN system is powered off.
Does the impedance change radically when the system is powered down?
the book states 62 kohm pull-down in parallel with 470 pF. I can't imagine that would draw enough power to keep the brake lights from illuminating.
Is this a faulty module? or is this normal and I need to add a large in-line resistor on all trucks in the field wired this way? Are XS2 modules the same way if this is normal?
eta: when I use a multi-meter on another XA2, I get 62K ohms between pin #15 and pin #38, so I am leaning twoards this being a bad module.
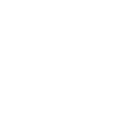
XC21/22/23 VREF supply Max Current
Hi, Appendix A in the manual states there are two VREF supplies for the XC2x range and it delivers 70mA current max. Is that 70mA per VREF (150mA total) or 70mA total across both VREF's?
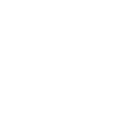
Odd XA2 voltage readings displayed on MD3
As you can see the Vref and +Bat are a bit off on MOD4.
any ideas?

XA2 Temperature Warning Threshold
Was wondering what the temperature threshold is on XA2 units before the internal temp will trigger a warning in the system?

IQAN-XC10 max output current exceeded
What happens if I try to drive a load that is greater than 2.5amps with the HS output of a XC-10?
Customer support service by UserEcho