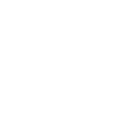
XA2 no connect four red LED blinks
I have an MD3 running a small program and an XA2 expansion module. When connecting only power , GND , Can-H, Can-L and ID tag #3 to the expansion module I get a four red LED blink with no Orange/ Yellow.
No connection message on the MD3.
The ID code in Iqan Deisgn is the same as ID tag.

Hi Anthony,
I am glad it was just a case mistaken identity and the XA2 module was in fact an XT2 module !
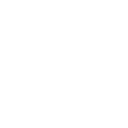
XC-23 minimum input voltage
Hello,
I have an H-Bridge that drives a DC brushed motor on 12V. I need to determine the PWM ratio being supplied to this motor by the H-Bridge. There is no other signal that could get me this information so I am contemplating hooking both sides of this motor to PWM inputs on the XC-23. Before doing such a thing, I looked at the signal using an oscilloscope. Basically, the signal is 0-12V most of the time but dips below 0V when the ON time finishes. The lowest voltage read with the scope is -11V for a short period of time.
There are no Absolute Requirements for negative voltages on inputs in the datasheet of the XC-23. What is the absolute minimum voltage that can be applied to a PWM input of the XC-23 without damaging it ?
Guillaume

Short Circuit Protection on XA2 DOUTs?
Pardon me if this information is already readily available but am having trouble finding it.
If the wiring for an XA2 DOUT is shorted to battery is there an internal protection strategy in the module that will protect the XA2 from being damage?
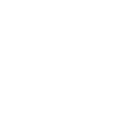
XS2 Dout to +bat?
I'd like to have IQAN control be paralleled with switch control. This specific application will be a drop axle. I want the IQAN to drop the axle in certain situations, and have a switch that will drop it at any time, even if the control system is powered down,
I believe I have to protect the module from back-feeding, correct? Will just diode protection be enough or do I need to have the Dout controlling a relay that would toggle the input between the switch and a +bat source?
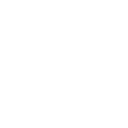
Low side outputs protection diode
Hello,
I need to drive relays on low side outputs on the XC-23 and MD4-5. Do I need to use relays with included coil protection diodes or if the outputs of these modules are already internally protected ?
Thanks,
Guillaume
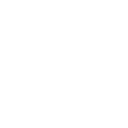
Using two(2) or more low side outputs in parallel on XC-23
Hello,
I'm wandering if I could use two(2) or more low side outputs in parallel on the XC-23 to increase the carrying current capacity from 300mA to 600mA (2 outputs) or more. I have a relay that I need to drive that needs more than 300mA.
Thanks,
Guillaume
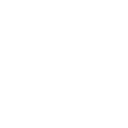
XC10 Multiple Address
I have a project that uses one MD3 and one XC10. The XC10 sits on its on Expansion Bus CAN line with no other devices except for the MD3. Occasionally, during startup the XC10 will report multiple address.
Currently we tell the customer to power cycle the machine if this comes up and it typically goes away. I am looking into automating this if possible. I have tried a few things and have not had any luck. Is there a way to do a forced reset either on the MD3 and/or XC10 to try and reset the error?
Right now, the XC10's V+ supply is behind a relay so I can cycle it power directly. Testing this method has also not panned out.
MD3 cycle time is at 10ms. I read on a different forum post that the XC10 can only go down to 20ms. Ideally, I want to keep the cycle time as low as possible because of how the machine operates. Would going to 20ms help with the multiple address issue?
Are there any othe XC10 limitations I should know about?
Is there anything else I can experiment with to try and resolve the multiple address without the user’s input?
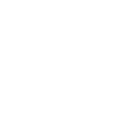
Why are extra flyback diodes necessary?
Why do the XA2 and XC10 manuals call for adding clamping (flyback) diodes to digital outputs?
From what I can gather, the modules are equipped with their own internal clamping diodes. Why would those be disabled for digital outputs?
Thanks
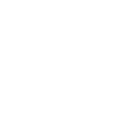
Digital Out instead of PWM for PULSAR Valves
Would any problems arise from supplying Parker Pulsar valves with a digital out signal instead of a PWM signal if proportionality is not desired? We're using an XA2.
Would a clamping diode be necessary in this configuration?
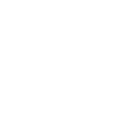
PWM output wiring
Why must a PWM output be wired as shown below in the XA2 manual?
When I've worked with mobile style PLC's in the past: It's just 1 pin for an output that delivers a PWM signal to a solenoid, then the other pole of the solenoid is wired to a common ground.
Why must there be three pins involved for this? Why shouldn't you wire one pole of the solenoids to a common ground (same potential as battery negative)?
Thanks in advance.
Customer support service by UserEcho