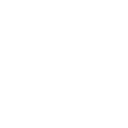
COUT open load error calculation
We have a machine that has sporadic nuisance open load errors on a function controlled by a unidirectional current output (COUT-G) on an MC43. Since this happens with some frequency, I suspect we are right up against the limit of the open load detection threshold. They test out well in assembly, but any increase in resistance occurring in the field might be setting it over the edge of the error threshold.
How can I calculate at what load resistance, commanded current, and supply voltage an open load error will occur?
This function is controlled with a Parker CCP024H 1/2" super coil with nominal resistance at room temperature of 30.30 ohms. Machine runs on 24V (around 28V when alternator charging). Maximum commanded current is set to 600mA.
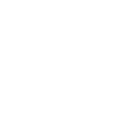
Using Current Out as 4-20 ma signal for VFD
Are the current out channels on an MC43 suitable for dishing out a 4-20 ma signal? It would be controlling a VFD.
I know the current out channels are typically used to control valves and used in the hundreds of milliamp range.

COUT overload error when PWM HS is shorted to GND
We are using a MC43 and using PWM and COUT channels. What we have noticed is when a PWM HS output is shorted to ground, one of our COUT outputs goes into overload. In our case, C2:51 was shorted to ground but C2:67/C2:15 had the overload error.
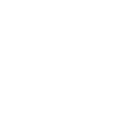
ID-Tag 4-7 for Molex MX123
Hello,
ID-tag 4 to 7 does not exist for Molex MX123.
We use 4,5 and 7 today and have to re crimp those ID-Tags for MX123.
When do you plan to offer ID-Tags 4 to 7 for MX123?
Regards
Fredrik Forsberg
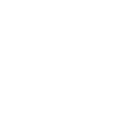
MC4X CAN bus labelling different in manual and IQAN Design
IQAN Design refers to CAN bus on the MC4X as A, B, C etc, manual (under installation) refers to it as numbers 1, 2, 3 etc. Although its obvious to work out, its better for us if its one designation across the board to avoid confusion when cross referencing documents.

MC41 losing CAN comms
We are using a MD4-7 and x2 MC41's on some of our machines (we actually wanted to use only x1 MC42 for these jobs but we are still waiting for the parts to arrive and have deadlines to meet so we are just using what we have available to get the job done)
But last night we started testing the machine and went through all of the procedures and functionality when all of a sudden an error appeared on the display telling me that one of the MC41 controller lost comms, but the other one was still fine and giving readings... So the 1st thing we tried to resolve this was typically switching the machine off and on, but this time there was no CAN comms at all.
We went though the wiring harness and made sure that everything was correct and the wiring was all good, so we then went and replaced both these controllers with new MC41's we had in stock, we plugged it in uploaded the software and the system was happy again with the new controllers and it is still working fine at this moment... So I took the 2 faulty MC41's to my office and connected it all together to try and diagnose the issue.
Each time I tried uploading software (using IQANDESIGN 5.01 via ethernet) it kept on warning me about the incomplete system and that only the MD4-7 will be updated.
Eventually we switched from CAN-A to CAN-B only on the MC41's. but upon each attempt to upload the software, the same "incomplete system" warning appeared.
So I just left it for a while and a few minutes later decided to just try again uploading once more. Well it worked all of a sudden and that is also a big problem, because I didn't change anything where I could say " there, that was the problem".
This is worrying us a bit, because we have no idea why this happened in the first place and secondly these machines are going to the middle of Africa... So this sort of thing must not happen at all!
I have only been using MD4's and MD3's with XA2's in the past without any problems at all, these are our first machines using the MC4x family and this is also the 1st time that I encountered any issues like this on IQAN.
Have anyone else experienced this before? I have no idea why it failed or why it started to work again and this is definitely not the correct answer to give the person asking this question when there are deadlines to meet.
The other thing to mention also is the LED's on the controllers which blinked bright yellow 3 times then blinked dimmed yellow 3 times while it was not communicating. which also does not correspond with these fault codes in the manual. There was no RED LED blinking at all.
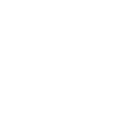
MC4x/XC4x 12V 30W solenoid overload error
What is the suggested solution for driving NG6 valves with standard 30W solenoids at 12V system voltage with MC4x/XC4x modules?
We use the HS+LS digital outputs for driving Parker D1VW valves with "K" code solenoids in a 12V system. As stated in the instrucion book, max load per output is 2.5A, but the measured current is 2.7A (as in the D1VW catalogue). The measured solenoid resistance is 5 Ohm, but it should be within 7-14 Ohm (MC4x/XC4x instrucion book).
30W solenoids are standard at other valve suppliers too, so changing the valve isn't an option. Change the system voltage to 24V also isn't possible for this project.
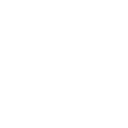
MC41 - M18-4 Barrel Speed sensor
Hi,
I have an MC41 module and I want to pick up the signal from a speed sensor M18-4VPFF200-Q8.
I want to measure the speed on the coupling between a motor and a torquemeter. I have a reflective sticker on the coupling, and I’m using this sensor to pick up the speed. However, when I connect the sensor, I’m reading zero on the MC41. I can see the lights on the sensor changing, which indicates the sensor is generating pulses, but the MC41 isn’t registering them.Here’s how I connected the sensor:
Sensor pin 1 (brown): 12V
Sensor pin 2 (white): GND
Sensor pin 3 (blue): C1:12 on the MC41
Sensor pin 4 (black): C1:11 on the MC41
The max speed I want to measure on the coupling is 200RPM. I calculated the max frequency as:
Thus I calculated my Max Frequency (Hz) = (Max RPM×Pulses per Revolution)/60 = (200*1)/60 = 3.33 ~ 3 Hz
Do you have any input on whether the issue might be software or hardware related?
Thanks!
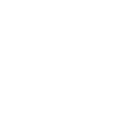
Master / Expansion Different -Batt
We have a requirement to have multiple XC43 modules remotely to the master MC43FS module. Its likely they will all be powered from separate power supplies and they wont supply the same 0V for batt -ve.
Is this likely to be a problem in terms of interference etc?
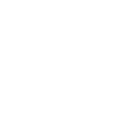
PWM Output Commanded to 0, but voltage measured at Output
IQAN Tech Support,
We are looking for help with troubleshooting our "IQAN Controller, Master Unit, IQAN - MC43" Safety Controller. It is getting inputs from two Temposonics tank-level sensors in our electronic water-level system, models GB Series & RF 5th Gen input sensors. The IQAN controller is PN 20085113.
We are receiving a potential difference (voltage output) of 0.39 V from Output pin to System Ground when measured with a multimeter; however the programming software indicates that the output should be 0 V. Our known inputs and outputs are below:
Inputs |
Outputs |
||||
I!: Inclinometer |
Connector 1, Pin 26 |
0 – 5 V |
O1: High |
Connector 1, Pin 48 |
0.24 V (Pin-to-Pin) |
I2: AFT Level Sensor |
Connector 1, Pin 53 |
4 - 20mA |
O2: Low |
System Ground |
|
I3: FWD Level Sensor |
Connector 2, Pin 33 |
4 - 20mA |
***SHOULD BE = 0.0 V Output*** |
- The tank level sensors are bottomed-out, as there is no water in the tank.
- With no water in the tank, the IQAN is programmed to output 0% Du Cycle, yielding 0.0 gallons on the display - but there is a .39V measured.
- The lowest water level reading that the sensors could output is 120 gallons, but should read 0.0 gallons below that.
- We are needing help troubleshooting and establishing / calibrating our 0.0 baseline
Questions:
1. Why is a voltage being read at the output, when the program is indicating that it should be zero?
2. Can we create a code or loop in the program to circumvent the small output voltage?
Customer support service by UserEcho