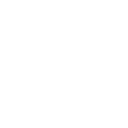
L90LS controller
l have an L90LS valve with proportional soleniods and would like to use a Joystick to operate which is the best choice out of parker range
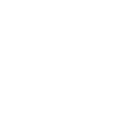
LED lamp and how is it controlled it via the program
where on the MC41 I connect LED lamp and how is it controlled it via the program

vdin buttons duration
Is it possible to adjust the default time that Vdin buttons when pressed and held remain 'on' for?
We have a multi-master application using a MD4-10 and a MD4-7. On each we have momentary buttons commanding functions that are slow in operation meaning the button has to be pressed for some time- By default the buttons while still pressed go to the 'off' state by Iqan even though still pressed requiring the user to press again- this is not acceptable to the user. We cannot latch the buttons for safety reasons. The buttons seem to switch to 'off' after about 10-12 secs on the MD4-10 but longer (approx 20 secs) on the MD4-7.
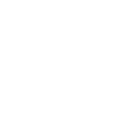
PWM Driver 5A
Has anyone had any experience whereby they have used a single IQAN PWM out with a 5A load ? The data sheets say "no" but I am just wondering if this is possible if the number of outputs used simultaneously, is controlled.
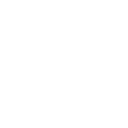
MC41 PWM out HS+LS flyback diode wiring question
I have a MC41 setup where I need to use a bidirectionnal CAM output in PWM mode to drive a bidirectional valve (2 coils). There is a mention to not use a flyback diode in closed loop control but is it ok to add diodes on coils if the outputs are used in PWM mode, not in current output? I tried it and it seems to work just fine.
I want to add diodes as there will be an emergency operation switch installed to directly power the coils. We want the diodes to prevent high voltage spikes to the MC41 module and the switches.
Found on the forum:
With IQAN-MC3 and IQAN-MC43, -MC42 and -MC41, the internal clamping diode is not disconnected when COUT pins are used as open control PWM.
Does that mean that we do not need to add diodes?
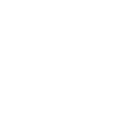
MD4 real time clock and internal temperature sensor issue
Hi,
I have several issue comes from a customer who run MD4/MC31 multimaster system.
They have MD4 who are not anymore able to keep the RTC.
To be sure, I took a kit apart and tested it myself. Finally, I move the MD4 alone and tried it with a very small program. Only value to show date/time/temp.
When it boot, the RTC is resetted and the temperature is OK (around 40 Celsius).
But when I update the date/time from iQanRun, the date and time appear to be OK, but the internal temp goes to -1C and give critical error.
I did a short video to show what I did and to show what's append.
Thanks!
There is some picture to complete:

Overload Errors when PWMOuts are Off
We have just updated from IQAN 3.19 to IQAN 4.06.
We are now seeing over load errors on several solenoids being controlled with PWM out signals.
The overloads only occur when the outputs are off. When they are on (90% Duty cycle) the errors go away.
I believe I remember reading something about circuit failure detection being active even when outputs are off as part of an IQAN 4 update.
Any recommendations on how this could be resolved?
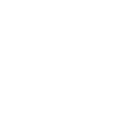
Reason for not using diode protection on COUT's?
What is the reason for not being able to use diode protection on COUT's? The manual for the MC3 for example states 'Do not install diodes across the coils', just wondering why this is noted, is there a specific reason?
Also there are a selection of other methods of suppression, resistors etc. Can resistors be used? In terms of diode suppression, is the TVS diode not to be installed in the same way as say a standard diode is not to be used?

MC43 RTC
Does the MC43 have a Real Time Clock? Does it need one?
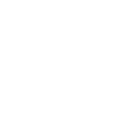
F3+F4+Up buttons problem in MD3.
I am using IQAN design V3.19.7.4013. When I pressed F3+F4+Up buttons in MD3 same time, openning the main menu page. But I don't want this. This is a problem for me. What can I do for this.
You can see this problem the following video.

Customer support service by UserEcho