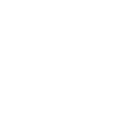
MD4 real time clock and internal temperature sensor issue
Hi,
I have several issue comes from a customer who run MD4/MC31 multimaster system.
They have MD4 who are not anymore able to keep the RTC.
To be sure, I took a kit apart and tested it myself. Finally, I move the MD4 alone and tried it with a very small program. Only value to show date/time/temp.
When it boot, the RTC is resetted and the temperature is OK (around 40 Celsius).
But when I update the date/time from iQanRun, the date and time appear to be OK, but the internal temp goes to -1C and give critical error.
I did a short video to show what I did and to show what's append.
Thanks!
There is some picture to complete:
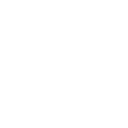
Looking for vehicle schematic example with display, controllers, joysticks and etc.
Need a good example of vehicle electrical schematic with Parker controls.

IQAN-LM 3D Models
I am just using up a couple of Legacy LM - 30 Joysticks that we have in stock and I could do with a 3D model for it - I was just wondering if anyone has one?

multiple camera input
Hi all
I have a new application requiring multiple SV cameras feeding into a MD4 master. I only need to view one or two inputs at any given time, but all four camera feeds need to be available and switchable at any time. I know i will have to use some form of ethernet switch for the multiple feeds into the C4 port of the MD4, but don't know if this needs to be a managed or un-managed switch? Has anyone out there done this sort of thing with the SV cameras, and if so can you help with the app file in the MD4 and recommend a suitable switch?
many thanks
A

Hello.
We have done some testing with rugged ethernet switches to see if they work with the MD4 and SV cameras.
They are unmanaged switches so you only connect them and are ready to go.
These two switches were tested with three cameras (only had 3 to test with) and was found to work.
Molex DRL-750Murr
Electronik Art.-No. 58160
Test were also done on 'Moxa TN-5305' and 'Phoenix Contact FL switch 1605 M12'.
These two switches experienced problems when more than one camera were added.

Overload Errors when PWMOuts are Off
We have just updated from IQAN 3.19 to IQAN 4.06.
We are now seeing over load errors on several solenoids being controlled with PWM out signals.
The overloads only occur when the outputs are off. When they are on (90% Duty cycle) the errors go away.
I believe I remember reading something about circuit failure detection being active even when outputs are off as part of an IQAN 4 update.
Any recommendations on how this could be resolved?
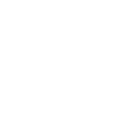
Resolution of PWM output
Hi!
When monitoring the output of the PWM it shows only values with no decimals although the input is with decimals. I have attached an example. Is it true that the resolution of the PWM output is discrete values?
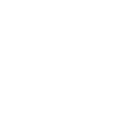
why PWM instead of COUT?
I am planning to drive a proportional relief valve (AP04G2YR 21C) with a XA2.
Is there any reason to use a PWM output over a COUT?
With COUT, I would think I would have open and short circuit detection (not sure about PWM) and it would take into account the coil heating up over time.
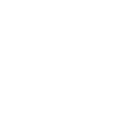
Ground triggered digital input
Is there a way to configure an XA2 expansion module's digital input to accept a ground triggered signal without adding external resistors? I have an application that requires a grounded input instead of a positive voltage.
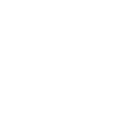
Reason for not using diode protection on COUT's?
What is the reason for not being able to use diode protection on COUT's? The manual for the MC3 for example states 'Do not install diodes across the coils', just wondering why this is noted, is there a specific reason?
Also there are a selection of other methods of suppression, resistors etc. Can resistors be used? In terms of diode suppression, is the TVS diode not to be installed in the same way as say a standard diode is not to be used?
Customer support service by UserEcho