No similar topics found.

0
Thanks
AXIS F1005-E camera with MD4
Paul Summers 11 years ago
in Other
•
updated by Ulrik Zakariasson (Software development) 11 years ago •
1
We have had great looking results utilizing an AXIS F1005-E camera and AXIS F41 main unit with an MD4 as a rugged backup camera for a mining prototype. The only down side it the components cost almost as much as the MD4!
The IP camera display functionality is a fantastic option!
The IP camera display functionality is a fantastic option!
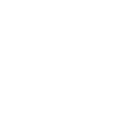
0
Answered
Is there a new MD3 display?
Im sure I have read somewhere on this site about an MD3 M32? is this a different display from part number 20072409?
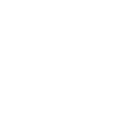
0
Answered
Piggyback on J1939 Backbone
Kelly Shuman 10 years ago
in Other
•
updated by Ulrik Zakariasson (Software development) 10 years ago •
4
I would like to know if there would be any issue using the J1939 backbone to support an IQAN master/slave network. Eventually, we would be reading the J1939 information also. I will verify that the bus load isn't too great. Is it good to add the other devices on the network to the program to avoid collisions?
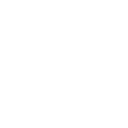
0
Answered
Two Md3 in the same CAN Bus
Masia Jean-Baptiste 10 years ago
in Master modules / MD3
•
updated by Gustav Widén (System support) 10 years ago •
5
Hello
It's possible to have two MD3 in the same CAN Bus ?
Have you a specification for this application ?
Thank
It's possible to have two MD3 in the same CAN Bus ?
Have you a specification for this application ?
Thank
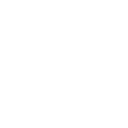
0
Answered
MC3 CAN, no contact and CAN error (bus off)
Masia Jean-Baptiste 10 years ago
in Master modules / MC3
•
updated by Gustav Widén (System support) 10 years ago •
1
Hello
What is the difference between this two Error codes ?
Thank
What is the difference between this two Error codes ?
Thank
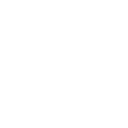
0
Adjusting voltage of COUT on an MC2
We are modifying an existing excavator for a technology demonstrator. We want to drive a proportional valve that was already on the excavator. We measured the voltage and current the machine was providing to the valve, and the peak voltage and current were 23V and .78A.
Using the COUT output from the IQAN MC2, I can adjust the current, but there does not seem to be any way to adjust the voltage. When we measure the voltage across the connector from the MC2, we only get 14V.
Any thoughts on how I can get the IQAN to match the output of the controller from the machine?
Thank you,
Graham
Using the COUT output from the IQAN MC2, I can adjust the current, but there does not seem to be any way to adjust the voltage. When we measure the voltage across the connector from the MC2, we only get 14V.
Any thoughts on how I can get the IQAN to match the output of the controller from the machine?
Thank you,
Graham
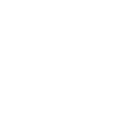
0
Answered
Difference between XC21, XC22 and XC23
What are the differences between these modules? There doesn't seem to be any information online or in IQAN Design user manual.
Thanks.
Thanks.

0
Answered
MC3 DOUT leakage current
Hello,
we connect MC3 to LED working lamp with DOUT channel.
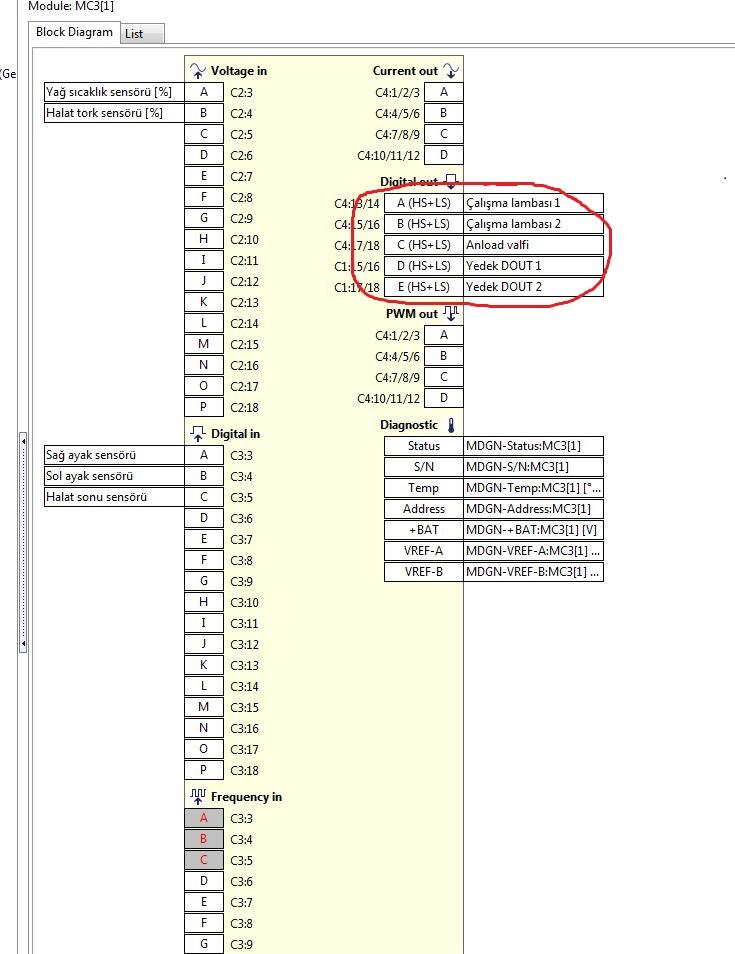
we connect MC3 to LED working lamp with DOUT channel. The Lamb current consumption is about 750mA. when its turn on.
The Lamb turn on its fine no problem. but it works very lackluster When turn of the light. You can see photo on the bottom of the description.
Now, Turn off the lights. So on the photo left lamp connect the C4 DOUT, right lamp connect the C1 DOUT.
these problem are just C4 but C1 DOUT works fine. What causes it?
Thank you.
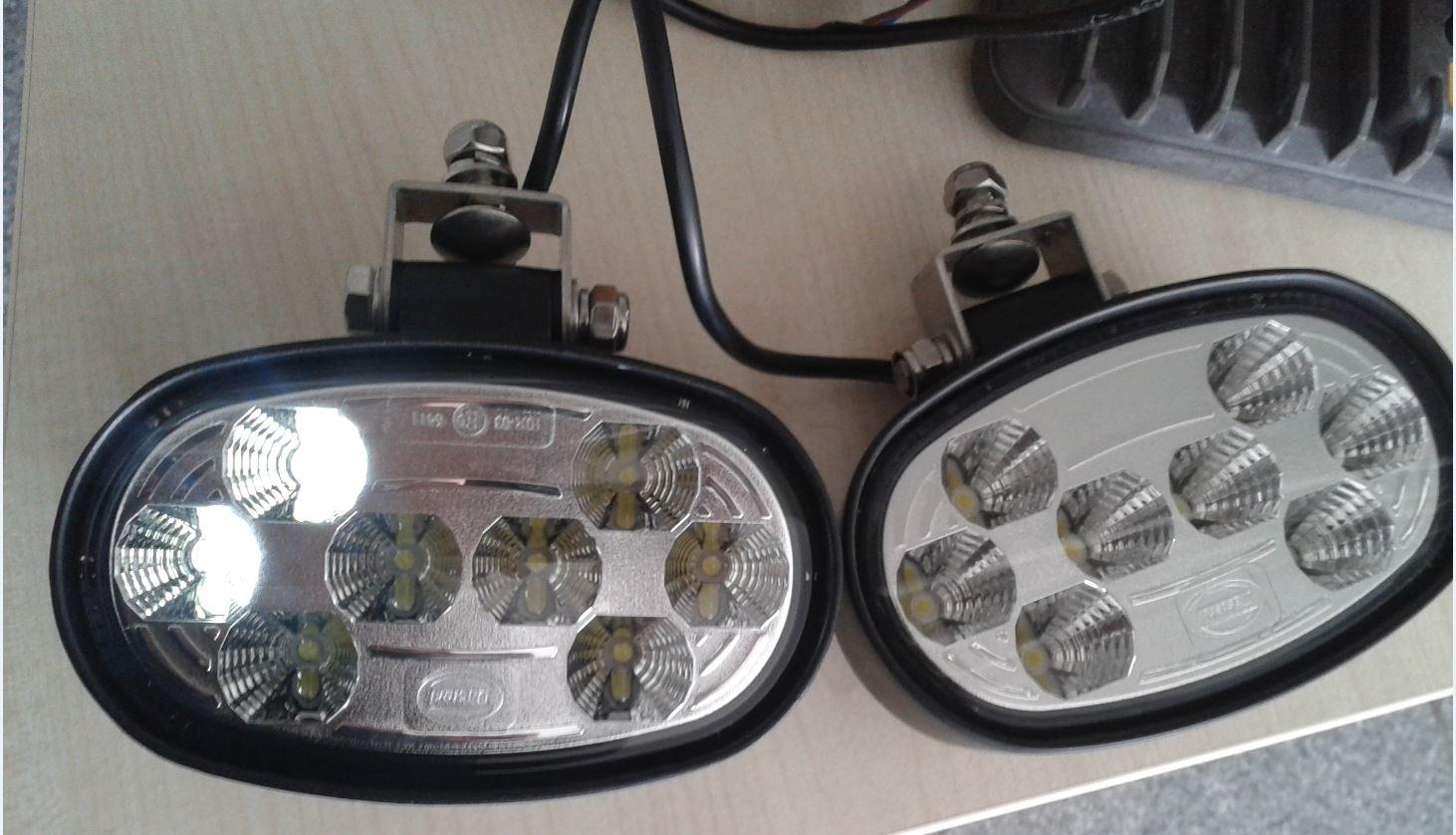
we connect MC3 to LED working lamp with DOUT channel.
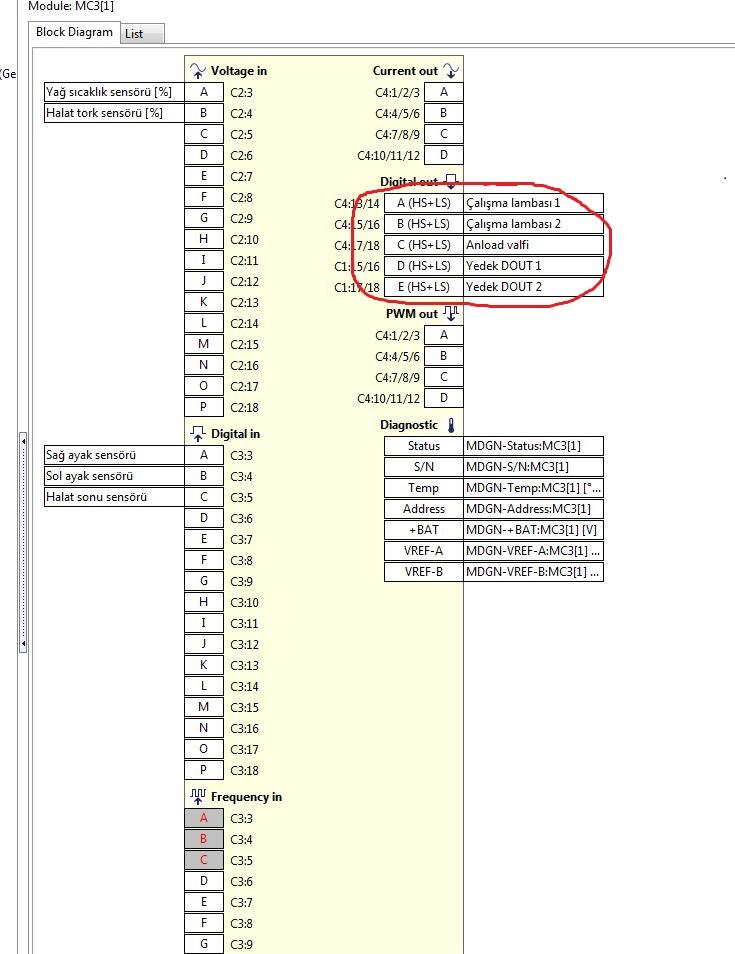
we connect MC3 to LED working lamp with DOUT channel. The Lamb current consumption is about 750mA. when its turn on.
The Lamb turn on its fine no problem. but it works very lackluster When turn of the light. You can see photo on the bottom of the description.
Now, Turn off the lights. So on the photo left lamp connect the C4 DOUT, right lamp connect the C1 DOUT.
these problem are just C4 but C1 DOUT works fine. What causes it?
Thank you.
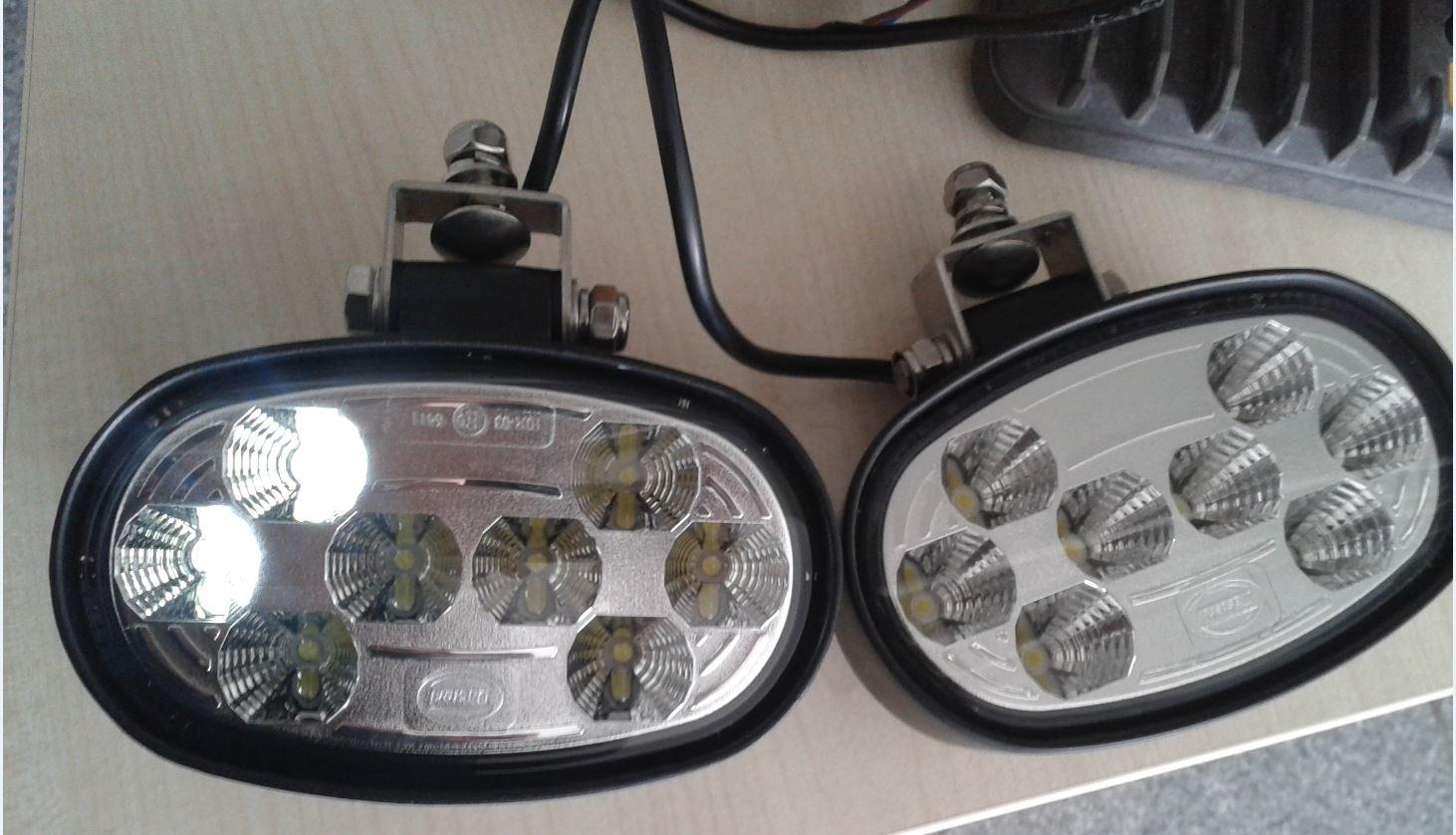
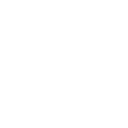
0
Completed
Problem with my system 1 MD4 and 2 MC3
Masia Jean-Baptiste 10 years ago
in Master modules / MC3
•
updated by Gustav Widén (System support) 9 years ago •
2
Hello everybody,
I have three problem in my system.
Can you help me ?
See above my configuration.
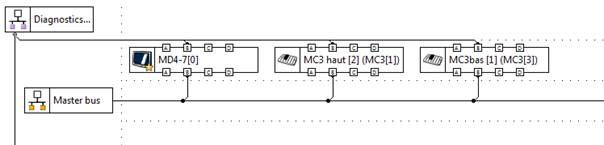
The first one:
In my system, when I supply the modules (1 MD4, 2 MC3), I don’t have any problem. When I power on the engine of the vehicule, sometimes the screen on MD4 is black and is blocked. No action is possible !!!!
The second:
When I power on my engine, sometimes I have an open load message in the MD4 on my Current out or Digital out on MC3. The wiring of the vehicule is good !!!!!
Do you have an idea on the two problems?
The third problem:
In my system I have a LED lights two colors (white and red) but I have three cable.
These leds work with low current ( less 200 milliamps ). We think that it will be possible with the “lowside” .
The first is the +VCC on the red light the second +VCC on the white light and the last is the ground for the two colors. One single LED works . When the red is on ( stop / brake ) the white is off . When he white is ON , the red is OFF.
How so you connects on the MC3 Digital Out?
I have three problem in my system.
Can you help me ?
See above my configuration.
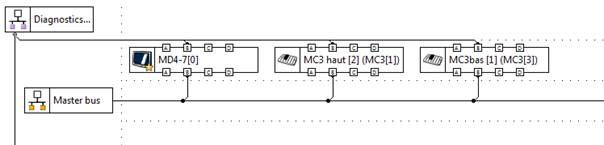
The first one:
In my system, when I supply the modules (1 MD4, 2 MC3), I don’t have any problem. When I power on the engine of the vehicule, sometimes the screen on MD4 is black and is blocked. No action is possible !!!!
The second:
When I power on my engine, sometimes I have an open load message in the MD4 on my Current out or Digital out on MC3. The wiring of the vehicule is good !!!!!
Do you have an idea on the two problems?
The third problem:
In my system I have a LED lights two colors (white and red) but I have three cable.
These leds work with low current ( less 200 milliamps ). We think that it will be possible with the “lowside” .
The first is the +VCC on the red light the second +VCC on the white light and the last is the ground for the two colors. One single LED works . When the red is on ( stop / brake ) the white is off . When he white is ON , the red is OFF.
How so you connects on the MC3 Digital Out?
Customer support service by UserEcho