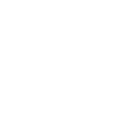
Can I have 24 Volt COUT if I have 12 Volt Power Supply?
I may have missed it in the training on IQAN Design, but is it possible for me to have a 24V COUT from an XC43
if I have only a 12V battery supply?

XA2
hello,
i am this XA2 error in one of our 7ech forklifts, the machine is fully operational, but this error keeps on popping up ‘VREF error Value 4.98v’ can anyone explain why?
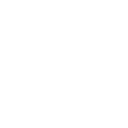
XA2 VREF supply more than 5V?
Hello,
I encountered a strange problem with XA2 module.
For some reason the VREF voltage fluctuate between 5 to 5,5Volts and due to that all the VIN-channels turns on simultaneously around 0 to 30% and the crane moves without touching levers.
Replacing XA2 module didn't solve the problem.
Is it possible that there could be some grounding issues in VREF circuit or has the MD3 display unit any affect on XA2 VREF circuit?
- Markus
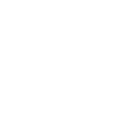
XC42 blink code R4:3 3:1:6
Hello,
We have a customer with this error pattern in one of the XC42 installed in the machine: R4:3 3:1:6
But we can’t find this pattern in the manual.
Can you explain what this blink code means, please?
Best regards
Adolfo
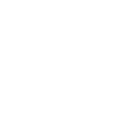
DOUT LS issue with LED
Greetings,
I have 4 LEDs each connected to a DOUT LS channel on an MC43.
The issue I have is they each turn on faintly even when the output is off.
Once the DOUT is on the light appears brighter.
The LEDS themselves are 12V LEDs like this one (though each is a different color):
https://www.factorymation.com/PDA-B12V-B
I don't currently have a Current Limiting Resistor inline, would not having that cause this sort of behavior?
Or is there something else I am missing about operating LEDs off the DOUT channels?
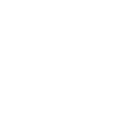
Wireless transmission of SV camera feed?
Has anyone had experience of wirelessly transmitting the camera feed between SV and MD4 using ethernet bridge or another method?
We have a customer that wishes to have a SV in a remote location a few hundred meters away from the screen and wireless is preferred due to the environment. I understand there would be an increase in latency but we can live with that.

Interested in IOT
I am interested in IOT of data. I have the MC43. What is the best way to get my data to the clients.
I need a hardware path and a cloud place for the data.
Thank you

CCC for Chinese Market
Hello
I am exporting
- Parker IQAN-MC43FS (20085123)
- Steuermodul Parker IQAN-XC43 (20085183)
- Bluetooth Adapter Parker IQAN G11 (20085100)
- Kamera Kit Parker IQAN-SV-120 (20085106)
to the chinese market for our new prototype facility. CCC is required for the import, otherwise we are faceing an almost impossible custom clearance to China.
Do you have CCC approval for the above products. What should we do when you do not have CCC???
Thanks
Andreas Pauly
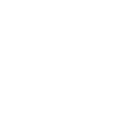
MD4-10 display turning white and can't communicate
Hello,
Our company's electric vehicle is using a MD4-10 display/controller with the IQAN software. Yesterday, the MD4-10 suddenly started to show lines of color on it and turned white. After a reboot, the screen seems to open but only showing a white screen and we are not able to communicate with it through an IQAN ethernet connexion.
We are trying to figure out what exactly happen so we do not repeat this mistake on the spare display that we have.
I believe something similar happen in 2015 on another post and it had to do with the supply being too low. But it was mentioned that that issue was fixed. Furthermore, we supply 12V to the Display with a 2 A fuse as well as the RTC protection circuit that is suggested in the manual.
- Our negative connexion is connected to the negative of the 12V battery through the vehicle's chassis. However, we also supply everything including another MD4-10 the same way. Could this cause this type of issue ? Does it need to be directly connected to the negative of the 12V battery?
- Can a short circuit between the power supply and the RTC input cause a fault of the screen, or just prevent the screen from being turned off?
Thank you for your support.
Best.
Customer support service by UserEcho