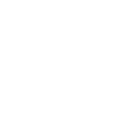
Digital out low side outputs
Is this MC43 output configuration is correct?
Can we power a load at higher voltage than the MC43 power for output 30 to output 46?
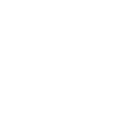
Reading Canbus through USB
I have the IXXAT USB to CAN V2 compact adapters along with a phoenix D-sub connector that has a resistor. I am tied into the diagnostics bus line (CAN-A-L and CAN-A-H) on the MD4-5 but I am not getting a CAN connection on IQANanalyze. This is my system layout:
I have a 4-pos deutsch connector for the G11 so I am using that for my USB Canbus adapter. I think I am missing something else.
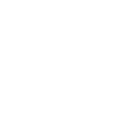
Fault Capacity of -VREF
In the IQAN MC4x/XC4x instruction book on page 67, it is recommended that sensors requiring a supply of more than 5V have their returns connected to -VREF instead of chassis ground. I understand the reason for doing this is to minimise sensor error, however, if the sensor supply is shorted to -VREF there will be a large fault current through the -VREF pin. What is the fault current handling capability of a -VREF pin? Furthermore, if this pin is not capable of handling high fault current for the time it takes for a typical thermal circuit breaker to trip, would powering the sensor from a digital output with current limiting be a preferred option?
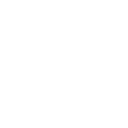
Parker UTS
Hi!
I have a question regarding the Universal Tilt Sensor:
We are to use a Parker UTS as shown in the picture below:
When reading the "Installation Sheet" regarding the mounting orientation it says:
Since we have a +/- 90 degree sensor I assume, from the picture, that it can be mounted "upside down".
However, when looking in the "User Manual" it says:
Since we have a 2-axis sensor this tells me that we can NOT mount it "upside down". From my perspective the two pictures contradict eachother when reading them separately. If I am supposed to combine the information from the two pictures my conclusion is that only +/- 90 AND 3-axis sensors can be mounted "upside down" but this seems a little too far-fetched. The information must be clearer than that.
Question: Considering the sensor we have, as shown in the first picture, can it be mounted "upside down"?
Also, while we are at it:
When reading the "User manual" under "3.1 Characteristics" I can not find our particular sensor that has Part.no: 169453ECD. Are there any differences between our V2.5 and V2 regarding the CAN messages or is the specification provided in the "User manual" also applicable to V2.5?
I hope you can shine some light on this matter. Thank you in advance!
Kind regards,
Christopher Fridstaden
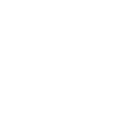
Can PWM outputs be programmed to send 0-10Vdc signal?
I have been doing some research and configuring a CANopen module to send a 0-10Vdc signal to run a prop valve. I have now been told that a PMW output on the MC4x and XC4x can be programmed to output 0-10Vdc. I wanted to confirm that is correct as I have seen in the forum that you are unable to send out that signal type.
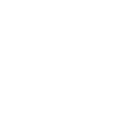
XC21 +BAT diagnostic value possible?
Is there a reason why the XC2x family of modules is missing +BAT diagnostic channel? I'm wondering if its a hardware limitation as the XA2 (below) and other modules appear to support it:
My customer needs to know the value of supply voltage on XC21 to read out on the master display. Unfortunately it needs to be a live readout rather than a digital flag if the module was to drop comms due to a low supply voltage. I will place a simple voltage divider circuit in if there is no workaround possible within the software but thought I would check first.
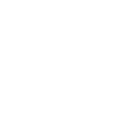
Motor control with MC41 in full bridge mode
What is the best way connect motor in full bridge mode to MC41?
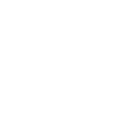
Output Switching Life
We are looking at the possibility of removing a reverse light flasher from our vehicle electrical system but have a question regarding the life of the High Side Digital Outputs.
Is there an expected lifespan of the Digital Outputs measured in Cycles or Switches?
The lights we would be controlling are 1.5Amp and would be Cycled at 1Hz.
Is there a concern with reducing the life of the digital output when used in this manner?
Thanks,
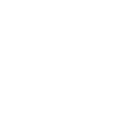
Controlling 9V/2.7A prop valve with MC4X
Has anyone tried to control a D1FBE01HC0NMWO (9V/2.7A spool) with a PWMOUT, if so what is the performance like? The rating for COUT is 2.5A so I will have to utilize the PWMOUT HS. I have read that COUTs allow the best performance with solenoid.
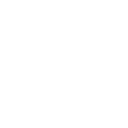
IP Cameras HTTP Streaming Phone Screen
I have a project where I am trying to stream a video of my cell phone to the MD4 display. As I want to be able to view google maps on the display for an in cab display.
I noticed in this post that it looks like the MD4s support HTTP streaming,
https://forum.iqan.se/communities/5/topics/295-md4-updated-list-of-tested-functional-ip-cameras
And I found this app that will do HTTP streaming via MJPEG
https://github.com/dkrivoruchko/ScreenStream
And then I get an access point connected from my Phone, PC, and MD4 display.
The phone has an ip address of 192.168.128.10:8080, and I can view the stream on the PC, but I cannot view it on the display.
I tried to type in "HTTP//192.168.128.10:8080" in the URL and that didn't work, and then I tried just the port of ":8080" in the URL.
Can you confirm that the MD4s support HTTP streaming and if so what port are you using, as I can change that in the app settings if its not 8080. And how would I configure this in IQAN
Customer support service by UserEcho